Making a Guitar Neck
Making a Guitar Neck
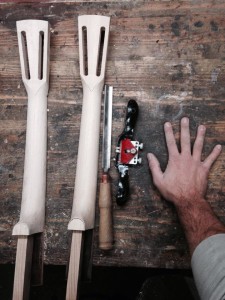
When the motivation to make a steel resonator guitar dropped in from above I had never cut a piece of metal, nor attached one piece of metal to another by means of tapping and threading, soldering, welding or the like. That was a big realm of experimentation. I breathed a sigh of relief, however, when it came time to carve the resonator guitar neck. When I was at Huss and Dalton guitars I carved the necks with Jeff Huss. I'd say I carved around 400 necks while I was there.
Although it was much like 'riding a bike' it was also much like re learning to ride a bike as things can be going smooth and then you get to a stop light that changes and you ungracefully fall over in front of people waiting for a green. It had been about five years since my time at H & D, and my first neck was shaped well but was much too thick. I thought I liked thicker necks but that one was overkill.
And so I began again.
It certainly didn't take long to get the feel back. A neck is a relatively complex shape, one because there are so many variations U/C/V, asymmetrical versions of them all and angles that affected fairly dramatically by the height of the neck. Notice how I didn't say thickness. I've heard it said that people 'buy horsepower but feel torque' and it's similar with guitar necks. People think they are buying 'thickness' thinking it means only the height of the neck, when really thickness involves the shoulders of the neck even more than you would think.
Unless a guitar is pretty darn thick, in most cases the inside of your hand never really grips the back of the neck. Try it, squeeze the palm of your hard against the neck of the guitar, it's fairly uncomfortable. And if it is touching its not really the height that may affect how your fingers can reach the frets, its the resulting shoulder that makes your fingers curl alllll the way around. Make that neck into a sharper V and you would notice it but not complain. What does in fact touch the neck most of the time is the base of your fingers and your thumb. They contact the neck in what I call the shoulder part of the guitar neck. This gives you the most important feedback from your hand about the shape of the neck. Of course the neck has to be a certain height and have a certain shape to get those shoulders where they are in a pleasing geometric fashion.
So I spend a lot of time on the area from the bottom of the binding to about a half inch above that. That's most likely where your fingers and thumb will end up, so I want to make it right.
After the neck has been rough set to that particular guitar and glued up it goes to the shaper. I had a custom shaper head made that is pretty gnarly. This will take the square blank to a rough round shape. I use a spoke shave next because it cuts quickly and cleanly, and is easy to keep consistently from one end to the other. Sometimes on hand carved necks you'll see a dip in the middle. That has to do with the stoke being naturally stronger in the middle than at either end. I keep the facets I'm carving along the length even by putting extra time in on the ends. The heel easily takes as much time as the whole neck does. It's such a complex curve, the way it curves up and out and comes to a point at the corner of the L. End grain is involved so extra time is spent sanding out those inevitable marks.
I use a Auriou rasp next to get the final shape, an Iwasuki file to clean of those marks and then orbital sand to 120, and then 220 grit. Wet the grain, let it dry then sand again. The rough work is done, then it's time to stain and put finish on them.
<iframe width="560" height="315" src="https://www.youtube.com/embed/c3QIG8GY8yI" frameborder="0" allowfullscreen></iframe>